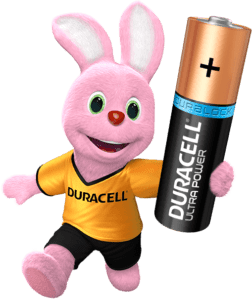
About Duracell
Duracell is the global market leader in the production of alkaline batteries, specialty and rechargeable batteries. Since the company was founded in the 1940s, it has grown to become an iconic brand when it comes to providing devices with power with compact and durable batteries. The company is known for its high quality and superior performance. The Duracell plant in Aarschot (Belgium) was founded in 1967 and nowadays it counts 450 employees. By 2020, it wants to be listed as a true “Industry 4.0 Factory”.
Therefore Duracell, Ometa and implementation partner Devoteam started an Industry 4.0 pilot project in 2017, to raise the quality of its batteries and the efficiency of the production process to a higher level.
Duracell’s Journey to Paperless Efficiency
In 2016, Duracell did a research to find out where the biggest losses were situated on the production floor. They conducted a content analysis on all kinds of data and documents that were used within the factory. The results indicated that each year they spend more than 20,000 hours on processing documents, both digital (Excel, pdf) as on paper. Therefore, the first thing to do was to eliminate all of this paperwork and Excel sheets. In order to do so, they found Ometa as a technology partner.
During the last 20 years, over 800,000 files were gathered in more than 156 different folders. Eventually, this created chaos and employees were hardly able to find the right documents. To cope with this problem, Duracell decided to implement SharePoint as a Document Management System (DMS). This allows the company to only work with current data and to eliminate 80% of the initial 800,000 files.
Untill recently, the typical flow was that documents were being filled in, after which a key-user entered the data into his or her system. The information was then printed out again and passed on to a planner or a technician. Why? Simply because it is impossible for operators on the shop floor to work with all of the underlying systems in which data is processed. Now however, thanks to the Ometa framework, this complexity is removed. Instead, all systems and documents are linked to each other in one central SharePoint platform.
All the information about production planning, production quantities, waste percentages, maintenance, safety and quality control which used to be processed manually in different places, now flows directly and automatically towards the digital workspace in SharePoint. This is how the information is now immediately available on the work floor.
Thanks to this real time connectivity of all data into a digital workspace environment, all exports and macros of any system towards Excel have become unnecessary. Instead, these are now replaced with real time portals. Whereas in the past, technicians needed to look and search for documents, they now get them delivered at the time when they need the information. Ultimately, for Duracell, working paperless has a huge positive impact on the speed of its factory. Moreover, this new way of working will allow the company to save about 650,000 euros over the next three years.
Success lies in the people
Two factors are very important in this transition. First of all, it is important to divide the project into manageable parts that you solve one by one. That is one of the biggest challenges. Secondly, you need the support of the entire company. You need the support of the management, you need strong leadership and need the cooperation of people on the work floor to get things going. This requires vision and organization.
For this project, Duracell has put together a ‘core team’ with staff who voluntarily participate. Especially the operators are involved in this project. It is not technically inspired and the people on the floor decide together with their team leaders what they find important. Engineering and IT follow that core team to achieve what is put forward. We always work with a lead model: we make a proof of concept and we work that out with input from several people.
After that, one or two teams test it out in reality and they then provide feedback. Based on this, the solution is rebuilt or optimized and only at that point the system is rolled out. We therefore proceed step by step and the input of the employees is very crucial. We also communicate a lot with the staff about this. The whole project is very interactive and the final application will not come as a surprise to our staff.